ã€Abstract】 The emission characteristics of mercury in coal-fired power plant are studied, and the mercury removal technique is briefly analyzed. The study found that most of the mercury produced by coal combustion remained in the bottom ash and flue gas of ESPs, accounting for about 42% and 39% respectively. The mercury emission in flue gas was mainly zero-valent mercury. In the wet process Most of the divalent mercury that is removed in the desulfurization system remains in the gypsum slurry, and there is less mercury residue in the desulfurization wastewater. According to the analysis and testing, the desulfurization system and the wet electricity system have a good removal effect on bivalent mercury. The denitrification system converts some of the zero-valent mercury into bivalent mercury and can remove part of the particulate mercury.
Key words coal-fired power plant; mercury; emission; mercury removal technology
1 Introduction
Mercury and its derivatives, which are highly toxic and persistent, transportable and bio-rich, can persist, migrate and spread globally in the atmosphere and the food chain, posing a great threat to the global environment and biosphere . As the highest level of the food chain, human beings suffer the most. Medical research shows that mercury damages human brain, spine, liver and kidney to varying degrees and affects people's perception, vision, taste and behavior. The morbidity and mortality of 178 species of birds in North America; the mercury content in polar fur over the 14th century; the contamination of fish, shellfish and shrimp; the maternal contamination of the fetus caused by pregnant women consuming methylbenzene The seriousness of In this situation, the formal signing of the Minamata Convention in Japan in 2013 marks a global consensus on mercury pollution control.
2 Research and Analysis
2.1 The form of mercury exists
Mercury released into the atmosphere from coal combustion is divided into three forms: 1) gaseous zero-valent mercury, also known as gaseous elemental mercury or gaseous elemental mercury, expressed as Hg0; 2) gaseous bivalent mercury, also known as "gaseous mercury oxide" HgCl2-based, expressed as Hg2 +; 3) particulate adsorption of mercury (non-discriminative valence state), expressed as Hgp. Different forms of mercury have unique physical and chemical properties, so their emission, transmission and deposition characteristics are also different. Due to the chemical nature of Hg0 is not active and very low water solubility and other characteristics, it is difficult to be captured. When it is released into the atmosphere, it stays for a long time and is transported away from the source as the atmosphere moves. However, Hg2 + is soluble in water and can be dissolved in the gypsum slurry of wet desulfurization equipment. Hg2 + is also easily adsorbed onto particulate matter and its residence time in the atmosphere is also short, generally settling near the source. Most Hgp can be removed with the capture of particles.
The factors affecting the morphological distribution of mercury in flue gas from coal-fired power plants are very complicated. The influence of coal composition is obvious. In addition, when the flue gas passes through flue gas purification equipment, some different forms of mercury will transform into each other. Coal-fired coal in our country is diversified, with various components accounting for different proportions. The form of mercury emissions from coal combustion also presents different states.
2.2 Mercury emission characteristics
Some studies have found that coal-fired power plant coal-fired mercury content of 17 ~ 385μg / kg, each power plant coal-containing mercury is quite different. The related tests and analyzes of mercury in a power plant show that the arithmetic average of the mercury content of the main mixed coal, large mixed coal and Huainan coal used in a coal-fired power plant is 213.1ng / g, and the distribution of mercury in different combustion products is shown in Fig.1.
Mercury removal
Figure 1 shows the mercury in the bottom residue, bottom ash ESP (referred to as bottom ash, the same below), gypsum (including desulfurization wastewater) and flue gas distribution. Mercury in the bottom slag is scarce, less than 0.1%, almost negligible; mercury is more distributed in ESP bottom ash, reaching 42.9%; and secondly in flue gas and gypsum slurry (including wastewater). In addition, according to the test, the main form of mercury in flue gas emissions is Hg0, accounting for 39.1%, while the most difficult to remove mercury form is Hg0. According to the theoretical and experimental study, wet desulfurization can remove a large amount of Hg2 +, so the gypsum slurry and desulfurization wastewater in the desulfurization system were tested and analyzed. According to the test results, mercury in gypsum slurry mainly exists in the form of Hg2 +; Hg2 + exists mainly in the form of HgSO4, and a small amount exists in the form of HgCl2 with a total mercury content of 285.6 μg / L, while total mercury in desulfurization wastewater Only 20.6μg / L, only 6.7% of the total mercury removal in the desulfurization system.
2.3 Related mercury removal technology analysis
According to the existing research, the technology of mercury removal from flue gas in coal-fired power plants shows that the existing mercury removal technology can be divided into the front of the furnace and the back of the furnace. Mainly refers to the use of clean coal washing coal and other clean coal technology, so that coal into the boiler combustion before the removal of most of the mercury, such as the use of foam flotation method for coal washing, so that the mercury content of coal can be reduced by 30% or more, and then use mild Pyrolysis method, so that mercury is heated evaporation, to further reduce the mercury in the coal removal efficiency of up to 80%. With these two clean coal technologies, coal can reduce mercury levels by 85% before it enters the boiler for combustion. However, the domestic coal washing rate before entering the furnace is very low, while the developed countries have more than 40% coal washing rate.
Desulfurization equipment (FGD) and wet electrostatic precipitator (WESP) have strong capability of removing mercury, especially the removal efficiency of Hg2 + reaches 89.66%. The removal capacity of Hg2 + [4-6,12] are mentioned. However, FGD and WESP have almost no ability to remove Hg0. As shown in the above table, Hg0 content increased after these two devices, which was not found in previous studies. According to the results of the mercury content test of the circulating slurry and wastewater in the FGD system, the circulating slurry contains most of Hg2 +, so it can be speculated that the flue gas carried a large amount of Hg2 + -containing slurry droplets into the WESP after passing through the FGD, Hg2 + environment in the reduction reaction occurred, and then generate Hg0, but the conclusion still needs further experiments to verify.
Injection Tooling & Mold Design
Professional injection molding customized products for 20 years, to provide you with a reassuring customized experience, in order to ensure product quality, the company strictly follows the ISO9001:2015 quality management system for management, one-stop service for assembly and packaging, free design for large quantities, affordable prices, and high quality Guarantee is your trusted source manufacturer.
Fast quotation, medical, electronic, automotive, household mold injection molding customization. Professional injection molding customized products for 20 years, to provide you with a reassuring customized experience. With many years of industry production experience, we can process and order according to drawings and samples, source manufacturers, quality assurance, complete specifications, high-quality after-sales service, modern complete sets of production equipment and superb workforce, with an annual production capacity of nearly 1,000 tons. Liquid silicone vulcanization molding equipment, injection molding process, extrusion/extrusion.
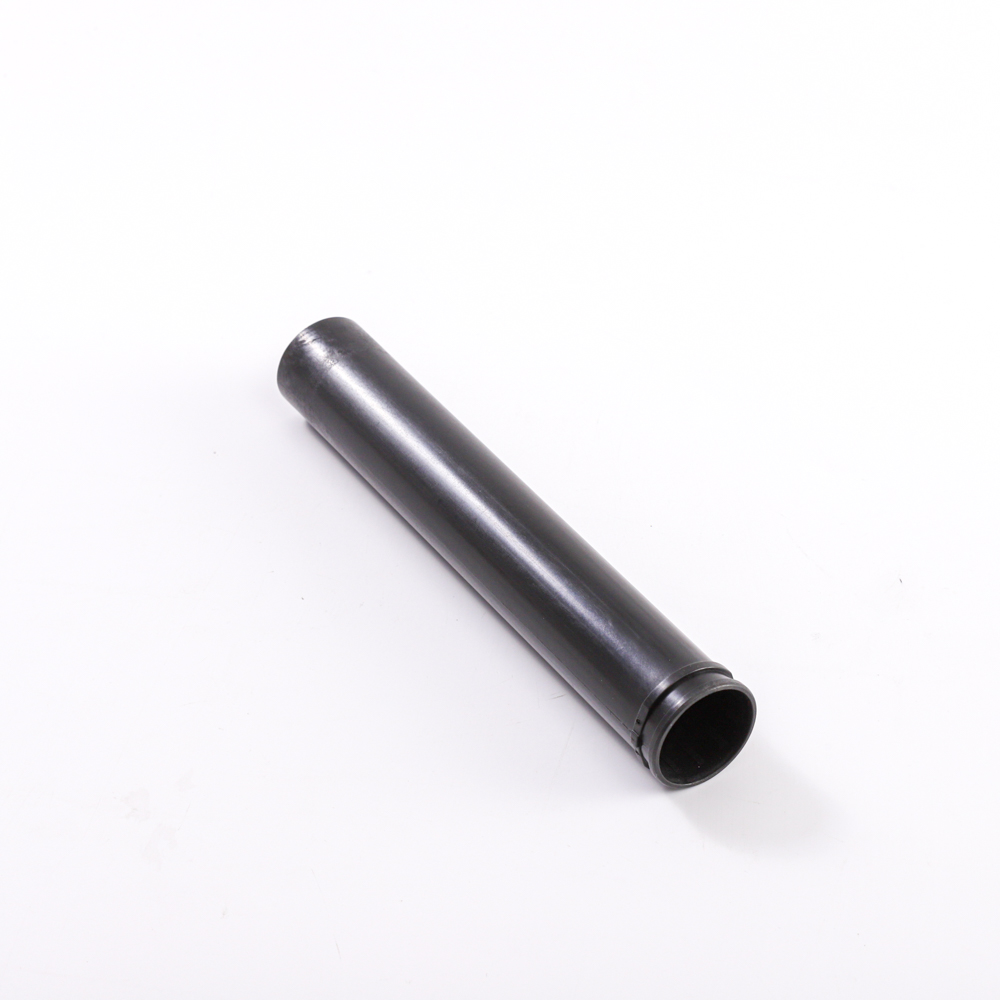
Injection Tooling & Mold Design,Injection Molding Tooling Design,3 Plate Injection Mold Design,Injection Molding Die Design
Suzhou Dongye Precision Molding Co.,Ltd. , https://www.sjdongye.com