If there is no hot air circulation system in the dryer, the equipment will not need to be moved after it is installed and adjusted. Although the dryer with a hot air circulation system is troublesome to adjust, its advantage of energy saving is obvious. The following uses some test data to illustrate. The measured working conditions of the drying unit are air temperature 15°C, hot air temperature 80°C, 2.2 kW fan, and standard air volume converted to 20°C 31 m3/min to 33 m3/min.
Determine the size of the hot air circulation first consider the solvent content of the gas in the drying system, because the organic solvent content in the gas reaches a certain concentration can cause an explosion. Table 1 lists the volumetric explosive concentrations of commonly used solvents.
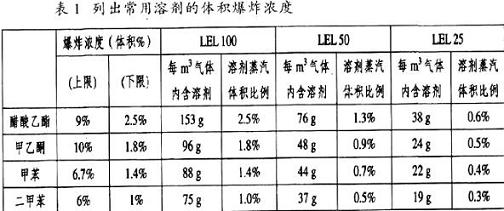
The volumetric explosion concentration of the solvent is divided into upper and lower limits, and concentrations between the upper and lower limits can cause explosions. The lower limit of explosion concentration is an important standard for dryer design. When LEL is used, LEL100 is the lower limit of explosion concentration. Some imported printers or complex machines, when the solvent vapor concentration in the gas reaches LEL25, the device buzzer will alarm, the device automatically stops running when the concentration rises to LEL50.
How much air flow does the dryer normally use to ensure safe operation? Counting it is clear. The amount of solvent evaporated in the unit time is the basis for the desiccator flow rate design. First calculate the volume of air required to dry 1000 grams of solvent. See Table 2.
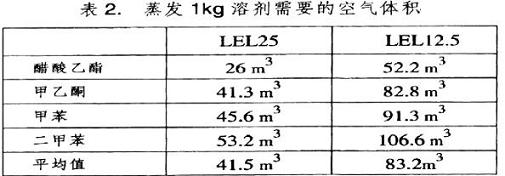
For example, if the concentration of ethyl acetate is LEL25, 38 g of solvent per cubic meter of gas, and 1000 g of 38 g of 26.2 m3 of water, then subtract the steam volume of 1000 g of ethyl acetate and dilute 1000 g of ethyl acetate into LEL25 with air. About 26 cubic meters of air are needed. Different solvent vapor volumes are different, and the lower explosive lower limit volume concentration is also different. Therefore, taking the average of the four solvents in the table, with the LEL 12.5 concentration as the design standard, 83 cubic meters of air are required for every 1 kg of solvent evaporated. According to the introduction of foreign contributions, the evaporation of 1 liter of solvent requires 74 cubic meters of air, and the proportion of commonly used solvents is about 0.9, which is consistent with our calculations, indicating that the LEL12.5 concentration is the design standard.
Next we discuss the dryer of the composite machine. The maximum dry base coating of the laminator is 4 grams per square meter, the working concentration is 25%, the compounding speed is 120 meters per minute, and when the width is 1 meter, the drying system evaporates 1440 grams of ethyl acetate per minute. The air flow of the dryer of the composite machine should be:
83×1.44=119.5 m3/min
Usually, the drying oven of the compound machine is divided into three sections, and the air volume of the centrifugal fan of each dryer is 119.5÷3≈40m3/min. The 120m speed compounding machine is equipped with a 30m3/min fan, so the speed will not exceed 80m when cooking bags, and the compound machine can still drive up to 120m when the coating weight is about 3g.
The above is only a rough estimate, which can be used for equipment configuration. The drying process is more complicated. For example, the evaporation of the three-stage drying oven will not be evenly distributed. Therefore, the adjustment of the circulation volume is very particular.
The hot air circulating dryer has three regulating valves, which are respectively an exhaust valve, a recirculating air valve and a fresh air intake valve. What people find surprising is that the main factor determining the recycling rate is the amount of exhaust air. Because the exhaust air volume of the drying system is always equal to the total amount of air intake, the total air intake volume mainly comes from the fresh air inlet, followed by the fresh air sucked by the negative pressure on the working surface of the drying oven (hot air jet surface).
The amount of air intake and the amount of exhaust air are related to the degree of "metabolism" of the gas in the drying system. The amount of air discharged from the dryer is generally slightly larger than the air flow from the hot air into the fan, but the air pressure may be lower. When adjusting the dryer, first adjust the exhaust valve until the negative static pressure of 400 Pa to 500 Pa near the exhaust butterfly valve in the exhaust pipe, the position of the exhaust valve remains basically unchanged, and then adjust the recirculating air butterfly valve. Because the circulating air duct is connected to the inlet of the centrifugal fan, the negative static pressure in the circulating air duct is higher than that at the discharge butterfly valve, so the hot air enters the circulating air duct after the circulating air butterfly valve is opened. The fresh air inlet can be understood as a "hole" opened in the circulating air duct. If the opening and closing degree of the recirculating air valve is not changed, the hole will be "plugged" and the air volume at the nozzle will be small; otherwise, if the hole is "leaked", the nozzle The air volume becomes larger.
Of course, this is a metaphor, and the problem is far more than simple. It also involves the distribution of the size of the pipes and the resistance of the pipes to the air volume. For example, there are no new air inlets on the circulation ducts of Italian equipment. The fresh air is sucked by the negative pressure of the drying oven. The hot air entering the circulating air duct has been mixed with a large amount of fresh air. Its circulation rate is controlled by the exhaust valve. Because the air volume of the system is equal to the intake air volume, the quantity of fresh air that is sucked in from the dry box population when the exhaust air volume is large is also large, whereas the amount of fresh air entering is small.
What is the role of the fresh air intake valve in the end? Compared with Italian equipment, most of the fresh air coming from the inlet of the drying box was moved into the fresh air inlet to avoid large amounts of air flowing to the bottom of the drying cabinet. This kind of airflow disturbance has a great impact on printing. The fresh air intake valve and the circulating air damper jointly regulate the hot air circulation rate. The general regulation rule is: when the circulating air damper is opened, the small fresh air intake valve must be closed. At this time, the hot air circulation rate is large; when the circulating air damper is adjusted, large fresh air is required. Air valve, the hot air circulation rate in this state is small, and the two air valves cooperate with the good sign that the nozzle air volume changes little.
Determine the size of the hot air circulation first consider the solvent content of the gas in the drying system, because the organic solvent content in the gas reaches a certain concentration can cause an explosion. Table 1 lists the volumetric explosive concentrations of commonly used solvents.
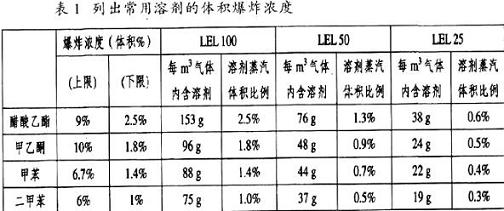
The volumetric explosion concentration of the solvent is divided into upper and lower limits, and concentrations between the upper and lower limits can cause explosions. The lower limit of explosion concentration is an important standard for dryer design. When LEL is used, LEL100 is the lower limit of explosion concentration. Some imported printers or complex machines, when the solvent vapor concentration in the gas reaches LEL25, the device buzzer will alarm, the device automatically stops running when the concentration rises to LEL50.
How much air flow does the dryer normally use to ensure safe operation? Counting it is clear. The amount of solvent evaporated in the unit time is the basis for the desiccator flow rate design. First calculate the volume of air required to dry 1000 grams of solvent. See Table 2.
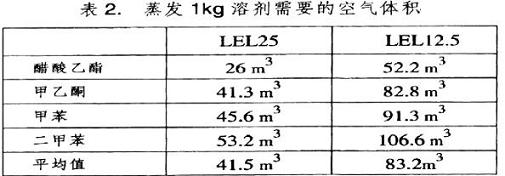
For example, if the concentration of ethyl acetate is LEL25, 38 g of solvent per cubic meter of gas, and 1000 g of 38 g of 26.2 m3 of water, then subtract the steam volume of 1000 g of ethyl acetate and dilute 1000 g of ethyl acetate into LEL25 with air. About 26 cubic meters of air are needed. Different solvent vapor volumes are different, and the lower explosive lower limit volume concentration is also different. Therefore, taking the average of the four solvents in the table, with the LEL 12.5 concentration as the design standard, 83 cubic meters of air are required for every 1 kg of solvent evaporated. According to the introduction of foreign contributions, the evaporation of 1 liter of solvent requires 74 cubic meters of air, and the proportion of commonly used solvents is about 0.9, which is consistent with our calculations, indicating that the LEL12.5 concentration is the design standard.
Next we discuss the dryer of the composite machine. The maximum dry base coating of the laminator is 4 grams per square meter, the working concentration is 25%, the compounding speed is 120 meters per minute, and when the width is 1 meter, the drying system evaporates 1440 grams of ethyl acetate per minute. The air flow of the dryer of the composite machine should be:
83×1.44=119.5 m3/min
Usually, the drying oven of the compound machine is divided into three sections, and the air volume of the centrifugal fan of each dryer is 119.5÷3≈40m3/min. The 120m speed compounding machine is equipped with a 30m3/min fan, so the speed will not exceed 80m when cooking bags, and the compound machine can still drive up to 120m when the coating weight is about 3g.
The above is only a rough estimate, which can be used for equipment configuration. The drying process is more complicated. For example, the evaporation of the three-stage drying oven will not be evenly distributed. Therefore, the adjustment of the circulation volume is very particular.
The hot air circulating dryer has three regulating valves, which are respectively an exhaust valve, a recirculating air valve and a fresh air intake valve. What people find surprising is that the main factor determining the recycling rate is the amount of exhaust air. Because the exhaust air volume of the drying system is always equal to the total amount of air intake, the total air intake volume mainly comes from the fresh air inlet, followed by the fresh air sucked by the negative pressure on the working surface of the drying oven (hot air jet surface).
The amount of air intake and the amount of exhaust air are related to the degree of "metabolism" of the gas in the drying system. The amount of air discharged from the dryer is generally slightly larger than the air flow from the hot air into the fan, but the air pressure may be lower. When adjusting the dryer, first adjust the exhaust valve until the negative static pressure of 400 Pa to 500 Pa near the exhaust butterfly valve in the exhaust pipe, the position of the exhaust valve remains basically unchanged, and then adjust the recirculating air butterfly valve. Because the circulating air duct is connected to the inlet of the centrifugal fan, the negative static pressure in the circulating air duct is higher than that at the discharge butterfly valve, so the hot air enters the circulating air duct after the circulating air butterfly valve is opened. The fresh air inlet can be understood as a "hole" opened in the circulating air duct. If the opening and closing degree of the recirculating air valve is not changed, the hole will be "plugged" and the air volume at the nozzle will be small; otherwise, if the hole is "leaked", the nozzle The air volume becomes larger.
Of course, this is a metaphor, and the problem is far more than simple. It also involves the distribution of the size of the pipes and the resistance of the pipes to the air volume. For example, there are no new air inlets on the circulation ducts of Italian equipment. The fresh air is sucked by the negative pressure of the drying oven. The hot air entering the circulating air duct has been mixed with a large amount of fresh air. Its circulation rate is controlled by the exhaust valve. Because the air volume of the system is equal to the intake air volume, the quantity of fresh air that is sucked in from the dry box population when the exhaust air volume is large is also large, whereas the amount of fresh air entering is small.
What is the role of the fresh air intake valve in the end? Compared with Italian equipment, most of the fresh air coming from the inlet of the drying box was moved into the fresh air inlet to avoid large amounts of air flowing to the bottom of the drying cabinet. This kind of airflow disturbance has a great impact on printing. The fresh air intake valve and the circulating air damper jointly regulate the hot air circulation rate. The general regulation rule is: when the circulating air damper is opened, the small fresh air intake valve must be closed. At this time, the hot air circulation rate is large; when the circulating air damper is adjusted, large fresh air is required. Air valve, the hot air circulation rate in this state is small, and the two air valves cooperate with the good sign that the nozzle air volume changes little.
Water Based Colorants For Wood Coating
Water Based Colorants; Water Based Pigment Paste; Water Based Color Paste
Guangzhou Quanxu Technology Co Ltd , https://www.skyelecteflonheater.com