Knowing how to use a product properly can significantly impact its performance and lifespan. For example, understanding the correct way to care for cast iron pans can make them last much longer. With electric motors, knowing the factors that influence motor life is the first step in extending their service life and reducing long-term costs.
**What does "end of life" really mean?**
In general, "end of life" refers to when a product no longer functions as intended. But what does this mean in practical terms?
End of life occurs when the motor can no longer meet the specifications listed in its data sheet—such as speed, torque, or accuracy. This means the motor might still be operational, but it’s no longer performing at the level it was designed for. If it can't fulfill its intended purpose, it becomes effectively "dead" for the user.
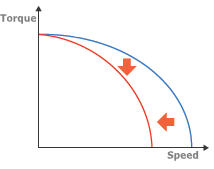
**What are the main factors that affect motor life?**
The lifespan of a motor typically depends on the first component that fails. The three most common components that fail first are bearings, gears, and circuit components such as drivers and controllers.
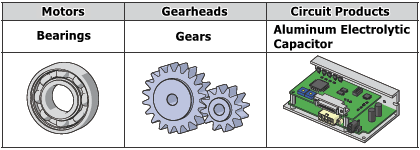
**Bearings**
Bearings are essential components that help reduce friction and control motion between moving parts. In a motor, they support the rotor and shaft. Since bearing failure can stop the motor from operating, they are considered critical parts.
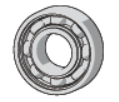
Inside an AC motor, bearings are crucial for smooth operation. The expected life of a standard motor is often based on the grease life within the bearings. Temperature plays a significant role here—exceeding radial or axial load limits can also shorten the motor's life. Motors with long-life grease can operate for up to 10,000 hours.
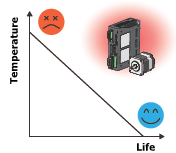
**Gears**
Gears are used to adjust speed and increase torque. They multiply torque based on the gear ratio and reduce speed accordingly. Like bearings, gears handle direct loads and can wear over time, especially under heavy or impact loads. Once worn, the motor may still run, but backlash and noise levels may exceed acceptable limits.
**Circuit Components**
Circuit products include drivers and controllers. These components manage the power and logic for motors like steppers and servos. Electrolytic capacitors within these circuits can degrade due to high temperatures, which directly affects the lifespan of the circuitry.
**How does temperature affect motor life?**
Temperature is one of the biggest factors influencing motor life. Motor life is often determined by bearing grease life, which is affected by temperature. A 15°C (27°F) rise in bearing temperature can cut its life in half. Similarly, electrolytic capacitors see their life reduced by half with a 10°C (18°F) temperature increase.
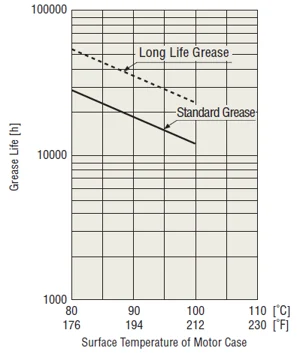
**How can heat be controlled?**
There are two main ways to control heat: cooling the source and reducing heat generation. Cooling methods include using fans, mounting on larger metal plates, or using heat sinks. Reducing operating temperature extends bearing life and increases duty cycle. I've worked on applications where water-cooled jackets were used to push a stepper motor's duty cycle close to 100%.
Another method is to reduce energy loss in the motor itself. High-efficiency or continuous-duty motors are good options. For steppers and servos, lowering current reduces temperature, though it must be balanced against torque requirements.
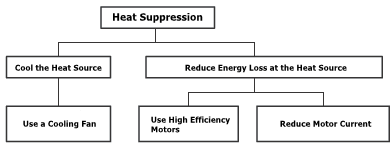
**Want to learn more about motor life and temperature effects?**
Check out our technical reference section for detailed information on service life, rated life, and calculation methods.
[Learn More About Service Life (PDF)](http://bsg-i.nbxc.com/blog/392581b92c5be34b949fac3f75f05985.png)
**Need help with cooling solutions, high-efficiency motors, or current optimization?**
Contact our experienced technical support team for assistance.
Electric Parts
Some of electric parts for Tower Crane:
1. Electric motor: Tower cranes use electric motors to power the lifting and rotation mechanisms. These motors convert electrical energy into mechanical energy to move the crane's various components.
2. Control system: Tower cranes require a sophisticated control system to manage the movement and operation of the crane. This includes controls for lifting, lowering, slewing, and trolleying.
3. Limit switches: Limit switches are used to set the maximum and minimum positions of the crane's various components. They help ensure safe and accurate operation by preventing the crane from exceeding its designated limits.
4. Power cables: Tower cranes require heavy-duty power cables to transmit electricity from the power source to the crane's electrical components. These cables need to be durable and capable of handling high voltage and current.
5. Circuit breakers: Circuit breakers are essential safety devices that protect the crane's electrical system from overloads and short circuits. They automatically interrupt the electrical current flow when a fault is detected, preventing damage to the crane and reducing the risk of electrical fires.
6. Transformers: Transformers are used to step up or step down the voltage of the electrical supply to match the requirements of the tower crane. They ensure that the crane receives the correct voltage for optimal performance and safety.
7. Sensors: Tower cranes often incorporate various sensors to monitor and control different aspects of their operation. These sensors can include load sensors, wind sensors, angle sensors, and anti-collision sensors. They provide crucial data to the control system, helping to ensure safe and efficient crane operation.
8. Emergency stop switches: Tower cranes are equipped with emergency stop switches that can quickly shut down the crane in case of an emergency or safety hazard. These switches are strategically located and easily accessible to crane operators.
Crane Electric Parts,Crane Anemometer,Tower Crane Electrical Parts,Encoder for Tower Crane,Frequency Inverter
SHEN YANG BAOQUAN , https://www.bq-cranes.com