High-purity metal is a product of modern integrated many high and new technology, although in the 1930s already a "high-purity substances," the name, but to improve the research and production of high purity metal to the important agenda, in the secondary After the World War, first of all, atomic energy research required a series of high-purity metals, and then with the development of semiconductor technology, aerospace, radio electronics, etc., the purity requirements of metals are getting higher and higher, which greatly promotes the development of high-purity metal production.
Purity has three meanings for metals. First, some properties and purity of metals are closely related. Soft pure iron, cast iron containing impurities is hard. On the other hand, impurities are very harmful. Most metals are brittle due to impurities. For semiconductors, very small amounts of impurities cause very significant changes in material properties. Niobium and silicon contain trace amounts of m, V group elements, heavy metals, alkali metals and other harmful impurities, which can seriously affect the electrical properties of semiconductor devices. Second, purity of the study will help elucidate the structure of beryllium emotional factors, influence of impurities on a metal material such defects, and thereby create conditions for the development of new materials and designs previously given material properties. Third, as the purity of metals continues to increase, the potential properties of metals will be further revealed. For example, ordinary metal ruthenium is the most brittle metal of all metals. In high purity, low temperature plasticity occurs, and ultrahigh purity has higher temperature superplasticity. The discovery of the potential performance of ultra-high-purity metals has the potential to broaden new application areas and open new breakthroughs in materials science, paving the way for the extension of high technology.
The purity of the metal is relative to the impurity, and the impurity in a broad sense includes chemical impurities (elements) and physical impurities (crystal defects). However, the concept of physical impurities is meaningful only when the purity of the metal is extremely high. Therefore, the content of chemical impurities is generally used as the standard for evaluating the purity of the metal, that is, the percentage of the main metal minus the total content of the impurities. Commonly used N (the first letter of nine). For example, 99.9999% is written as 6N, and 99.99999% is written as 7N. Further, the semiconductor material is also expressed in terms of carrier concentration (atom/cm 3 ) and low-temperature mobility (cm 2 V -1 S -1 ). The metal has a residual resistivity RRR and a purity level R (Rein heitgrad). There is no uniform standard for the definition of purity in the world. In general, the theoretical pure metal should be pure and completely free of impurities and have a constant melting point and crystal structure. However, any metal in technology does not reach the absolute purity without impurities, so pure metal has only a relative meaning, it only indicates the current technical standards. As the level of purification increases, the purity of metals continues to increase. For example, high-purity metal impurities in the past 10- 6 (parts per million), while the impurities ultrapure semiconductor materials up to 10-9 level (parts per billion), and gradually developed into 10-12 level ( One trillionth of a percent). At the same time, the purification difficulty of each metal is not the same. For example, in semiconductor materials, 9N or more is said to be high-purity, while refractory metals such as tungsten and tantalum are 6N, which is ultra-high purity.
High purity metal preparation is usually carried out in two steps, namely purification (primary purification) and ultrapurification (final purification). Production methods are broadly divided into chemical purification and physical purification. In order to obtain high-purity metals and effectively remove impurities that are difficult to separate, it is often necessary to use chemical purification and physical purification, that is, chemical purification while physically purifying, for example, hydrogen can be used as a shielding gas when silicon is melted in a flawless region. If a small amount of water vapor is added to the hydrogen, the water chemically reacts with boron in the silicon to remove boron which cannot be removed by physical purification. In addition, when vacuum melting is used to purify high melting point metals such as ruthenium and osmium , in order to decarburize, it is sometimes necessary to mix a slight excess of oxygen or to deoxidize a certain amount of carbon. This method is also called chemical physics. Purification. [next]
First, chemical purification
Chemical purification is the basis for the preparation of high purity metals. The impurities in the metal are mainly removed by chemical methods. In addition to directly obtaining high-purity metals by chemical methods, the purified metals are often first made into intermediate compounds (oxides, halides, etc.), and the intermediate compounds are distilled and rectified. , adsorption, complexation, crystallization, disproportionation, oxidation, reduction and other methods to purify the compound to a very high purity, and then reduce to a metal, such as germanium, silicon, germanium tetrachloride, trichlorosilane, silane (SiH 4 ) as The intermediate compound is purified and then reduced to bismuth and silicon. There are many chemical purification methods, and the commonly used ones are listed in Table 1.
Table 1 Â Common chemical purification method | |
method | content |
precipitation | Including precipitation, coprecipitation, uniform precipitation, etc. |
Metal replacement | Including the metal active order K , Ca , Na , Mg , Zn , Fe , Ni , Sn , Pb , H , Cu , Hg , Ag , Au , replacing the latter metal from the salt solution with the front metal |
extraction | Including organic solvent extraction, complex extraction, extractive distillation, etc. |
Ion exchange | Including the exchange of ion exchange resins, ion exchange fibers, ion exchange membranes and zeolites |
Electrochemical method | Including electrolysis, controlled potential electrolysis, electrodialysis, electrophoresis, etc. |
Compound purification | Including chemical transfer reaction, first compound is purified and further purified by thermal decomposition, hydrogen reduction, metal thermal reduction, oxidation, electrolysis, chromatographic separation, etc. |
Distillation | Including atmospheric distillation, vacuum distillation, steam distillation, azeotropic distillation, sub-boiling distillation, rectification, atmospheric sublimation, vacuum sublimation, etc. |
Recrystallization | Including recrystallization in water and other organic solvents, stepwise crystallization, etc. |
Chromatographic separation | Including gas chromatography, liquid chromatography, thin layer chromatography, dry column chromatography (purified by adsorption on activated carbon as the adsorbent, silica gel, alumina, molecular sieves, diatomaceous earth, etc.) |
filter | Including microporous membranes, ultrafiltration membranes and other media filtration |
Second, physical purification
Physical purification mainly uses physical processes such as evaporation, solidification, crystallization, diffusion, and electromigration to remove impurities. The physical purification methods mainly include vacuum distillation, vacuum degassing, regional melting, single crystal method (see chapter of semiconductor materials), electromagnetic field purification, etc., in addition to space-free gravity purification method.
Vacuum conditions are very important during physical purification. High-purity metal refining and purification are generally carried out in high vacuum and ultra-high vacuum (10 -6 ~ 10 -8 Pa). The important role of vacuum in the metallurgical process is: 1 to create favorable metallurgical reactions with gaseous products. Chemical thermodynamics and kinetic conditions, so that the metallurgical process that is difficult to separate impurities from the main metal under normal pressure can be realized under vacuum conditions; 2 reduce the solubility of gaseous impurities and volatile impurities in the metal, and correspondingly reduce its The content of the main metal; 3 reduce the temperature required for the volatilization of the metal or impurities, increase the separation coefficient between the metal and the impurity; 4 reduce or avoid the action of metal or other reactants and air, and avoid contamination of the metal or alloy by the gas phase impurities. Therefore, many purification methods, such as vacuum melting (vacuum induction melting, vacuum arc melting, vacuum electron beam melting), vacuum distillation, vacuum degassing, etc., must be carried out under vacuum.
1. Vacuum distillation Vacuum distillation is the use of a difference in vapor pressure and evaporation rate of the main metal and impurities from the same temperature under vacuum conditions to control the appropriate temperature to selectively volatilize and selectively condense a metal to purify the metal. Method, this method was previously mainly used to purify certain low-boiling metals (or compounds) such as zinc , calcium, magnesium , gallium , silicon, lithium , selenium , tellurium, etc. With the development of vacuum and ultra-high vacuum technology, Especially for the development of metallurgical high-temperature and high-vacuum technology, vacuum distillation is also used for the purification of rare metals and metals with higher melting points such as antimony, chromium , antimony , vanadium , iron, nickel and cobalt .
The main process of distillation is evaporation and condensation. At a certain temperature, the substance has a certain saturated vapor pressure. When the partial pressure of the substance in the gas pressure is lower than the vapor pressure of the saturated vapor pressure at that temperature, the substance evaporates continuously. The evaporation condition is to continuously supply the heat of the evaporated material and discharge the generated gas; the condensation is the reverse process of evaporation, and the saturated vapor pressure of the gaseous substance decreases with the temperature drop, when the partial pressure of the gaseous component is greater than its condensation temperature When saturated vapor pressure, the substance condenses into a liquid phase (or solid phase), and in order to carry out the condensation process to the end, the heat released by condensation must be discharged in time. The main factors affecting the vacuum distillation purification effect are: 1 the vapor partial pressure of each component, the larger the partial pressure difference, the better the separation effect; 2 the evaporation and condensation temperature and kinetic conditions, the general temperature decrease can increase the metal and impurities The difference in vapor pressure improves the separation effect; 3 the composition of the metal to be purified, the lower the impurity content of the original metal, the better the separation effect; 4 the interaction between the metal and the evaporating and condensing materials requires the evaporation of the condensed material itself to have the lowest saturated vapor. Pressure; 5 metal residual gas interaction; 6 distillation unit structure; 7 vacuum distillation is available in both å©åŸš and å©åŸšless, citrus-free distillation generally suspends the metal melt by electromagnetic field (see Figure 1), For the distillation process, please refer to the refining process of the above elements. [next]
2. Vacuum degassing Vacuum degassing is the process of removing gaseous impurities from metals under vacuum conditions. It is actually to reduce the solubility of gaseous impurities in the metal. According to Sivez's law, the solubility of a diatomic gas in a metal at a constant temperature is proportional to the square root of the partial pressure of the gas. Therefore, increasing the degree of vacuum of the system is equivalent to lowering the partial pressure of the gas, that is, reducing the solubility of the gas in the metal, and part of the gaseous impurities exceeding the solubility will escape from the metal and be removed. Taking the vacuum heat treatment of tantalum powder as an example, under high vacuum (2.5-6μPa), the moisture of the crucible is rapidly evaporated at 100-200 °C, and the hydride decomposition occurs at 600-700 °C. The alkali metal and its compound are at 1100-1600 °C. Volatilized at temperature, most of the iron, nickel, chromium, etc. are volatilized in the form of low melting point oxides, and nitrogen volatilization occurs at 2300 ° C. Compared with hydrogen and nitrogen with a large affinity for metal, carbon deoxidation is added ([C] + the [O] = CO ↑) and one or more impurity metal suboxides MeO n, manner. Vacuum degassing is widely used for purification of high melting point metal of tungsten, molybdenum, vanadium, niobium, tantalum, rhenium or the like.
3. Regional melting zone smelting is a method of deep purifying metal. The essence is to form a narrow melting zone by locally heating the slender ingot, and moving the heater to make the narrow melting zone move slowly along the ingot in a certain direction, using impurities in The difference in equilibrium concentration between the solid phase and the liquid phase. During repeated melting and solidification, the impurities are segregated into the solid phase or the liquid phase to be removed or redistributed. The melting zone is generally controlled by electric resistance heating, induction heating or electron beam heating. Figure 2 is a schematic diagram of the melting of the crucible region.
[next]
Fig. 3 is a partial phase diagram of the melting zone. When the solid-liquid equilibrium coexists, the concentration C s of the impurity in the solid phase and the concentration C 1 in the liquid phase are different, and the ratio of the two is called the equilibrium partition coefficient, that is, K. 0 = C s /C 1 . In Fig. 3, when the melting zone moves slowly from left to right, the impurity with the distribution coefficient K 0 <1 is enriched in the liquid phase, and gradually migrates to the right with the melting zone and is enriched; the impurity of K 0 >1 Then migrate to the right and enrich. Usually, when the primary smelting cannot achieve the required purity, the purification process needs to be repeated a plurality of times, or a series of heaters are used to produce a plurality of melting zones on the ingot to achieve high purification.
Regional melting is widely used in the purification of semiconductor materials and high melting point metals such as tungsten, molybdenum, niobium and tantalum, and is also used for the purification of high purity aluminum, gallium, germanium , copper , iron, silver and other metals. For cesium containing about 1 × 10 -3 % of impurities, after purification in the region for 6 times, the impurity concentration of the high-purity lanthanum portion can be reduced to 1 × 10 -3 %. After the tungsten single crystal is melted in 5 zones, the R 298 K/R 4.2K can be increased from 40 to 2000.
4. Electromigration Purification Electromigration refers to the separation of metal and impurity ions in a certain direction under the action of an electric field or the speed of diffusion to achieve the purpose of separating impurities. It is a newly developed method for deep purification of metals, which is characterized by the effect of separating interstitial impurities (especially oxygen, nitrogen, carbon, etc.), but is currently only applied to the purification of small amounts of metals. It can be combined with other purification methods to obtain ultra-high purity metals.
When the rod sample is galvanically flowed, the parent metal and the impurity ions move in a certain direction, and the drift speed of the ions is:
V=UF
High quality Aluminum core , aluminum plate&bar oil cooler core/air cooler core/water cooler core, can be customized designed, as every requirement is unique. Plate&bar Aluminum cores are widely used in the heat exchangers of Agriculture &Forestry Machinery, auto&vehicle, compressor, construction machinery, power generator and other high performance applications because they offer excellent thermal transfer capacity combined with small size and lightweight.
Customize cooler core upon your specification requirement.
Fins: Plain Fin , Perforated Fin , Wavy Fin , Louvered Fin , Serrated Fin
Structure: Plate&bar, plate-fin
Aluminum Core : High strength, high heat conductivity,high safety coefficient.
Supersonic Cleaning: High efficiency,little corrosion to metal , few pollution.
Vacuum Brazing : Strict control of vacuum degree, temperature and time.
Test : Air tightessn test, Hydraulic Pressure Test, 100% passed.
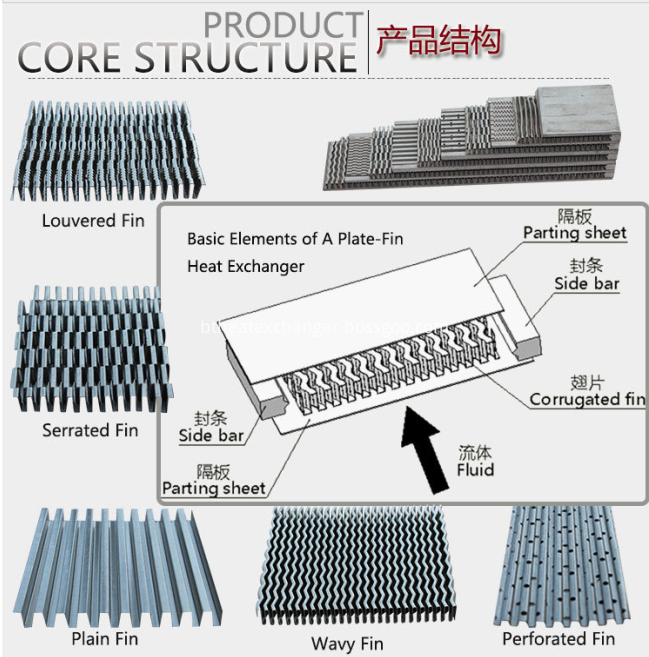
Bar Plate Aluminum Cooler Core,Aluminum Bar Plate Heat Exchanger Core,Oil Cooler Core,Water Cooler Core,Radiator Core,Air Cooler Core
Wuxi Better Technology Co., Ltd , https://www.btheatexchanger.com