Knowing When to Use Sensors for Robotic Welding
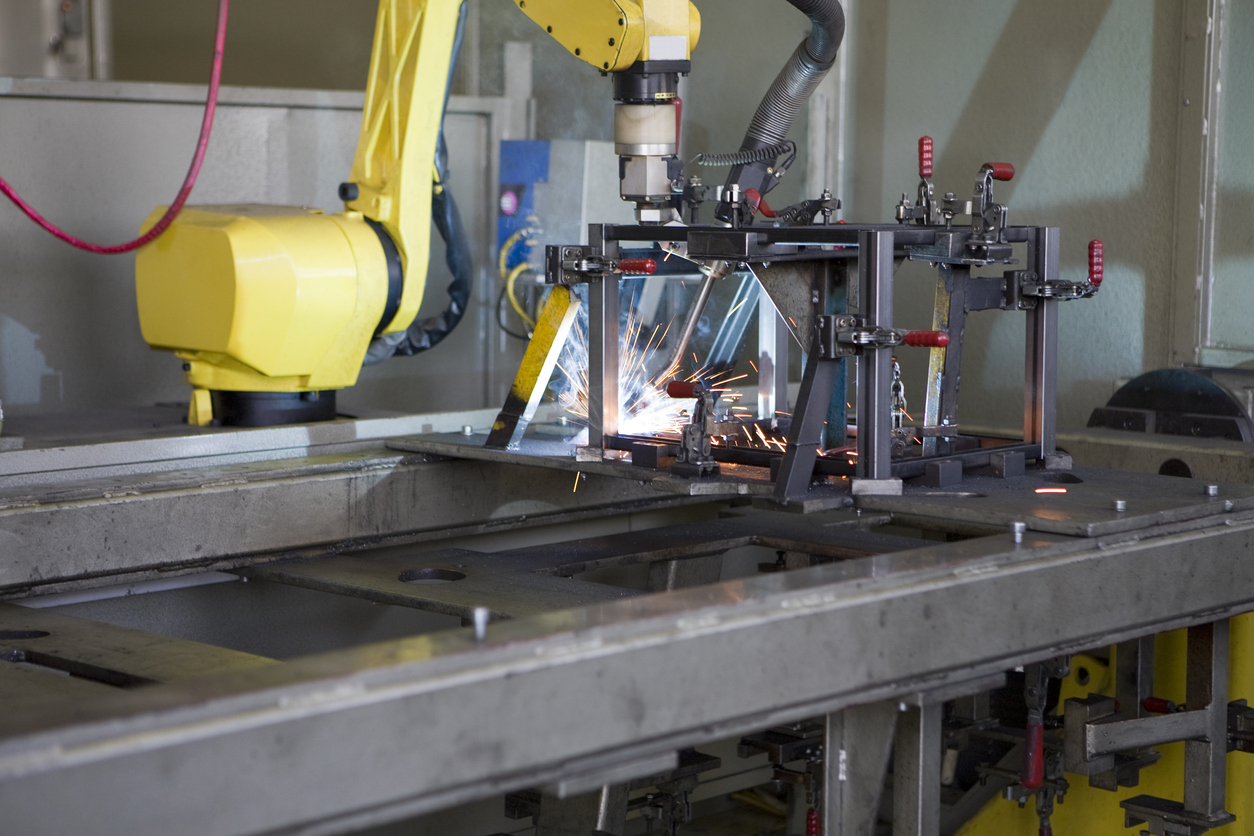
Robotic welding is a powerful tool that brings precision and efficiency to manufacturing. However, the true potential of robotic welding can be unlocked with the use of sensors. These devices provide robots with real-time feedback, allowing them to adapt to variations in parts, improve accuracy, and even learn from previous welds. This added intelligence makes robotic welding systems more flexible and reliable than ever before.
With so many types of sensors available, it can be challenging to determine when and which ones are worth investing in. The decision depends on several factors, including part complexity, production volume, and the need for consistent quality. Choosing the right sensor can make a big difference in performance and return on investment.
Types of Robotic Welding Sensors
As robotic welding has grown in popularity across various industries, different sensor technologies have been developed to address common challenges. Some of the most widely used sensors include:
- Touch Sensors: These sensors work by making contact between the welding torch and a specific point on the part. This helps the robot identify the exact location, ensuring precise weld placement. Touch sensors are especially useful in applications where alignment is critical.
- Seam Tracking with Arc Sensors: For arc welding, these sensors monitor the weld seam and detect any deviations from the programmed path. They allow the robot to adjust its movement in real time, maintaining consistent weld quality even if the part is slightly misaligned.
- 2D and 3D Camera Sensors: Vision-based sensors are highly effective at guiding robots to the correct welding position. While they may face challenges due to bright light during welding, they offer fast and accurate positioning, reducing errors and improving overall efficiency.
These are just a few examples of the sensors available. Each has its own advantages and is suited to different welding scenarios.
When Does It Make Sense to Invest in Robotic Welding Sensors?
Sensors are most beneficial in environments with high part variety, where the robot must perform multiple complex tasks. They are also essential when dealing with large or irregularly shaped components that are difficult to position consistently. If standard fixtures or tooling cannot compensate for part variations, then sensors become a necessary addition.
Before making an investment, it’s important to evaluate the expected ROI. Sensors can significantly boost productivity and reduce rework, but their cost should align with the benefits they bring. In cases where the savings from improved accuracy and efficiency outweigh the initial cost, sensors are a smart choice.
For more insights into robotic welding integration and how to choose the right sensors, consider consulting experts like Genesis Systems. With over 35 years of experience, they have helped countless companies implement efficient and reliable robotic welding solutions.
Posted in Robotic WeldingThe sample pulverizer that is working for trail plant, it is small capacity mill crushing the material. The working system way is vibrating grinding type. The material will load into the bowl, there is crushing ring and crushing hammer inside, in high speed rotation way the bowl will have vibrating and grinding function, will crushed to 80-200 mesh sample size by crushing ring and crushing hammer in 2-6 mintues, make it for testing directly.
Mining Lab Equipment,Sample Making Pulverizer,Vibrating Lab Grinding Mill,Sample Grinding Pulverizer Mill
henan ascend machinery , https://www.ascendminingcrusher.com