Knowing When to Use Sensors for Robotic Welding
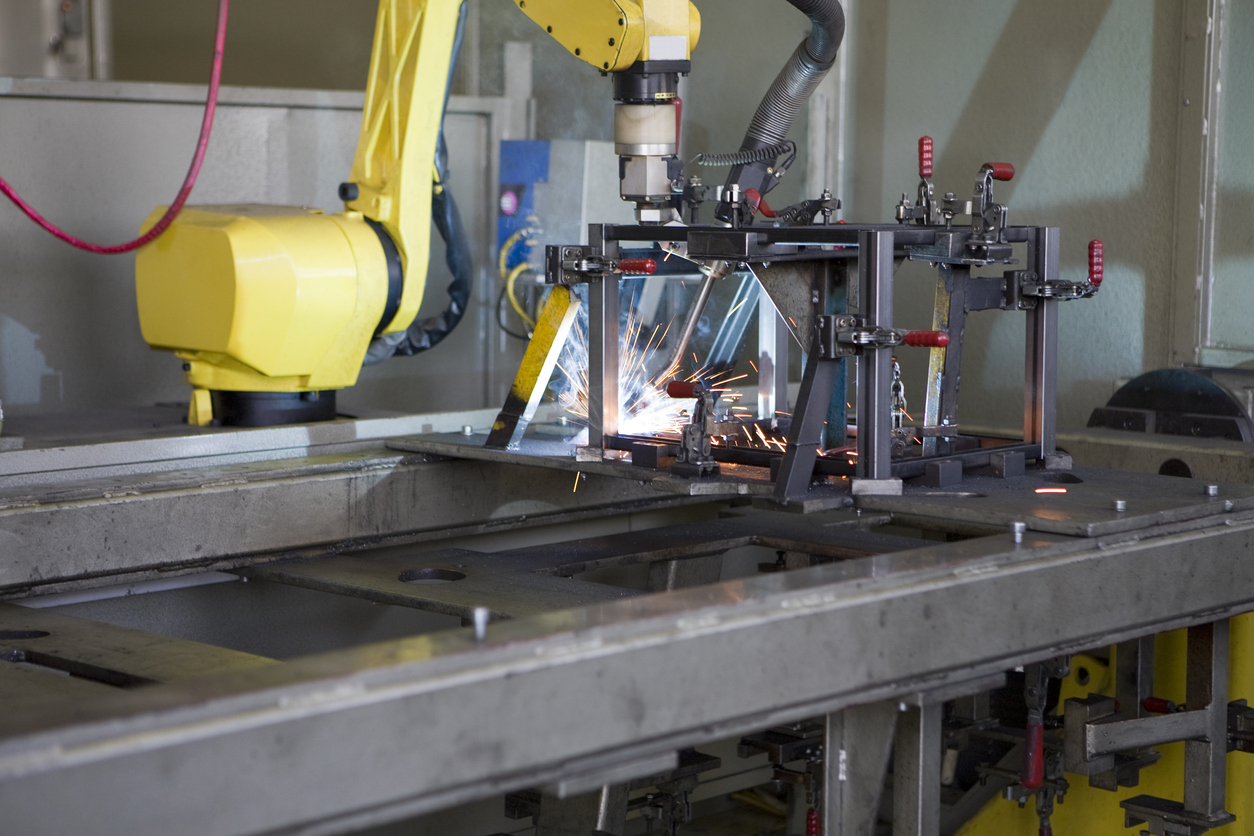
Robotic welding systems have revolutionized manufacturing by offering precision, speed, and consistency. However, even the most advanced robots can benefit from additional intelligence through the use of sensors. By equipping a robotic welder with sensor technology, you can significantly improve its performance, adaptability, and reliability in complex environments.
There are various types of sensors available for robotic welding, each designed to address specific challenges in the welding process. Choosing the right sensor depends on your application, the complexity of the parts being welded, and the level of accuracy required. Understanding which sensors are appropriate for your needs can help you make an informed investment that delivers long-term value.
Common Types of Robotic Welding Sensors
As robotic welding has evolved, so too have the technologies that support it. Here are some of the most commonly used sensors in modern robotic welding applications:
- Touch Sensors: These sensors are ideal for applications where physical contact is necessary. They work by detecting when the welding torch makes contact with a part, allowing the robot to adjust its position for precise alignment. This is particularly useful in situations where high accuracy is essential.
- Seam Tracking Sensors (Arc Sensors): Designed for arc welding, these sensors monitor the welding path in real-time. If the robot deviates from the intended path, the sensor detects the change and adjusts the movement accordingly. This ensures consistent, high-quality welds even when there are minor variations in the workpiece.
- 2D and 3D Vision Systems: Camera-based sensors provide visual feedback, helping the robot locate the correct welding point. Although they may be affected by the bright light from the welding arc, they are highly effective in guiding the robot and reducing errors caused by misalignment or inconsistent part placement.
These sensors not only enhance the performance of robotic welding systems but also reduce the need for manual intervention, increasing overall efficiency.
When Should You Invest in Robotic Welding Sensors?
Sensors are most beneficial in environments where part variation is high, or where multiple weld positions require precise control. For example, if your production involves a wide range of part designs or irregularly shaped components, sensors can help the robot adapt and maintain quality without requiring extensive reprogramming.
If your current setup relies heavily on jigs or fixtures to hold parts in place, and those tools aren’t sufficient to handle variations in part presentation, then integrating sensors could be a game-changer. Additionally, consider the return on investment—sensors can pay for themselves through increased productivity, reduced scrap, and fewer rework cycles.
Investing in robotic welding sensors isn’t just about improving accuracy—it’s about future-proofing your operations. As manufacturing becomes more automated, having smart, adaptable systems will be key to staying competitive.
For more insights into how robotic welding systems can be optimized with sensor technology, explore robotic welding integration services from Genesis Systems. With over 35 years of experience, Genesis has helped countless manufacturers achieve greater efficiency and precision through advanced robotic solutions.
Posted in Robotic WeldingSpiral Classifier,Fine Spiral Classifier,Ores Spiral Classifier,Gold Spiral Classifier
henan ascend machinery , https://www.ascendminingcrusher.com